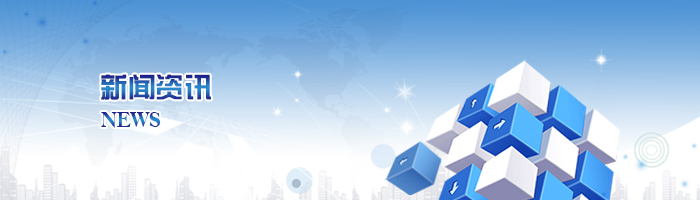
TP321,UNS S32100 ,1.4541,X6CrNiTi 18-10
TP321,UNS S32100 ,1.4541,X6CrNiTi 18-10 | |
Material No. | 1.4541 |
EN symbol | X6CrNiTi18 10 |
AISI/SAE | 321 |
UNS | S32100 |
AFNOR | Z 6 CNDT 18-10 |
B.S. | 321 S 31, 321 S51, 321 S18; 321 S 12 |
Standards | ---- |
Description
Alloy 321 (UNS S32100) is a titanium stabilized austenitic stainless steel with good general corrosion resistance. It has excellent resistance to intergranular corrosion after exposure to temperatures in the chromium carbide precipitation range of 800 – 1500°F (427 – 816°C). The alloy resists oxidation to 1500°F (816°C) and has higher creep and stress rupture properties than alloys 304 and 304L. It also possesses good low temperature toughness.
High carbon steels prone more to intercrystalline attack in weld zones and slower cooling sections. This steel avoids such attacks through its stabilization with Ti. The corrosion behaviour of this alloy in natural environments is very similar to the TP 304/304L alloys. Architecturally, it may not be adequate for near industrial or onshore locations in Europe. Satisfactory in many low-chloride waters, it is prone to pitting or crevice corrosion in seawater. Water treatment, galvanic protection and deaeration can influence the performance.
The annealing temperature range for Type 321 is 1800 to
2000° F (928 to 1093° C). While the primary purpose of annealing is to obtain
softness and high ductility, this steel may also be stress relief annealed
within the carbide precipitation range 800 to 1500° F (427 to 816° C), without
any danger of subsequent intergranular corrosion. Relieving strains be annealing
for only a few hours in the 800 to 1500°F (427 to 816° C) range will not cause
any noticeable lowering in the general corrosion resistance, although prolonged
heating within this range does tend to lower the general corrosion resistance to
some extent. As emphasized, however, annealing in the 800 to 1500° F (427 to
816° C) temperature range does not result in a susceptibility to intergranular
attack.
For maximum ductility, the higher annealing range of 1800 to 2000° F (928 to 1093° C) is recommended.
When fabrication chromium-nickel stainless steel into equipment requiring the maximum protection against carbide precipitation obtainable through use of a stabilized grade, it is essential to recognize that there is a difference between the stabilizing ability of columbium and titanium. For these reasons the degree of stabilization and of resulting protection may be less pronounced when Type 321 is employed.
When maximum corrosion resistance is called for, it may be necessary with Type 321 to employ a corrective remedy which is known as a stabilizing anneal. It consists of heating to 1550 to 1650° F (843 to 899° C) for up to 5 hours depending on thickness. This range is above that within which chromium carbides are formed and is sufficiently high to cause dissociation and solution of any that may have been previously developed. Furthermore, it is the temperature at which titanium combines with carbon to form harmless titanium carbides. The result is that the chromium is restored to solid solution and carbon is forced into combination with titanium as harmless carbides.
When heat treatments are done in an oxidizing atmosphere the oxide should be removed after annealing in a descaling solution such as a mixture of nitric and hydrofluoric acids. These acids should be thoroughly rinsed off the surface after cleaning.
Chemical composition (%)
C | Mn | P | S | Si | Ni | Cr | Mo | Ti | N | Nb | |
TP321 | 0.080 | 2.00 | 0.045 | 0.030 | 1.00 | 9.0-12.0 | 17.0-19.0 | 5x%C max.0,70 | |||
1.4541 | 0.080 | 2.00 | 0.040 | 0.015 | 1.00 | 9.0-12.0 | 17.0-19.0 | 5x%(C+N) max.0,70 |
Mechanical Properties:
Grade | Tensile Strength | Yield Strength 0.2% | Elongation -% in 50 mm (min.) | Hardness | Hardness |
ksi (min.) | Offset ksi (min.) | (Brinell) MAX | (Rockwell B) MAX | ||
321 | 75 | 30 | 35 | 217 | 90 |
1.4541 | 75 | 30 | 35 | 217 | 90 |
Convert ksi to Mpa Formula: ksi/0.1450377
Welding filler for welded pipe & tube |
S32100ER321 S32180, W32140 ------- ER347 S34780, W34740 1.4316, 1.4551, 1.4576 can be easily welded and processed by standard shop fabrication practices.. |
Main fields of application(depending on the specific conditions of use) |
Good resistance to hydrogen sulphide gas and intergranular corrosion coupled with good high temperature strength make 321 a suitable material for applications as tubes in heating furnaces and heat exchangers in sulphurisation and hydro-treating plants. In the petrochemical industry the steel is used in cracking furnaces for the production of ethylene and vinyl chloride. It is also frequently used for heat exchangers and piping in the chemical and petrochemical Aerospace – piston engine manifolds |