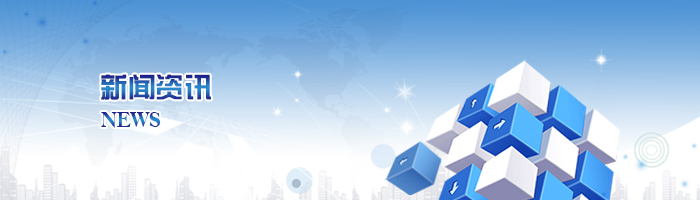
TP347,TP347H,UNS S34700, S34709,1.4550, 1.4912,X6CrNiMo18-10,X7CrNiNb18-10
TP347,TP347H,UNS S34700, S34709,1.4550, 1.4912,X6CrNiMo18-10,X7CrNiNb18-10 | |
Material No. | 1.4550/1.4912 |
EN symbol | X6CrNiNb18-10 X7CrNiNb18-10 |
AISI/SAE | 347/347H |
UNS | S34700/S34709 |
AFNOR | Z6CNNb 18.10 |
B.S. | 347S31/347S51 |
Standards | ---- |
Description
Alloy 347 is a stabilized, austenitic, chromium steel containing columbium which allows for the elimination of carbide precipitation, and, consequently, intergranualr corrosion. Alloy 347 is stabilized by the additions of chromium and tantalum and offers higher creep and stress rupture properties than alloy 304 and 304L which may also be used for exposures where sensitization and intergranualr corrosion are of concern. The addition of columbium also allows Alloy 347 to have excellent corrosion resistance, even superior to that of alloy 321. 347H is the higher carbon composition form of Alloy 347 and demonstrates improved high temperature and creep properties.
Alloy 347 can be used in air up to 850°C (1560°F) and in steam up to 750°C (1380°F). It is suitable for use in mild synthesis gas up to about 550°C (1020°F),Creep behaviour should also be taken into account when using the steel in the creep range.In flue gases containing sulphur, the corrosion resistance is reduced. In such environments this steel can be used at temperatures up to 600-750°C (1110-1380°F) depending on service conditions. Factors to consider are whether the atmosphere is oxidising or reducing, i.e. the oxygen content, and whether impurities such as sodium and vanadium are present.
Chemical composition (%)
C | Mn | P | S | Si | Ni | Cr | Mo | Ti | Cb/Ta | ||
TP347 | 0.08 | 2.00 | 0.04 | 0.030 | 0.75 | 9.0-13.0 | 17.0-20.0 | min:10xC max: 1.0 | |||
TP347H | 0.04-0.10 | 2.00 | 0.04 | 0.030 | 0.75 | 9.0-13.0 | 17.0-20.0 | min:10xC max: 1.0 | |||
1.4550 | 0.08 | 2.00 | 0.04 | 0.015 | 1.00 | 9.0-12.0 | 17.0-19.0 | min:10xC max: 1. |
Mechanical Properties:
Grade | Tensile Strength | Yield Strength 0.2% | Elongation -% in 50 mm (min.) | Hardness | Hardness |
ksi (min.) | Offset ksi (min.) | (Brinell) MAX | (Rockwell B) MAX | ||
TP347 | 75 | 30 | 35 | 201 | 95 |
TP347H | 75 | 30 | 35 | 201 | 95 |
1.4550 | 75 | 30 | 35 | 201 | 95 |
Convert ksi to Mpa Formula: ksi/0.1450377
Welding filler for welded pipe & tube |
*The weldability of Alloy 347 is good. Suitable welding methods are manual metal-arc welding with covered electrodes and gasshielded arc welding with the TIG and MIG methods as first choice. Preheating and post-weld heat treatment are not normally necessary. *Since the material has low thermal conductivity and high thermal expansion, welding must be carried out with a low heat input and with welding plans well thought out in advance so that the deformation of the welded joint can be kept under control. If, despite these precautions, it is foreseen that the residual stresses might impair the function of the weldment, we recommend that the entire structure be stress relieved. See under "Heat treatment". |
Main fields of application(depending on the specific conditions of use) |
Alloy 347 is frequently used for the fabrication of equipment, which must be placed in service under severe corrosive conditions, and is also common to the petroleum refining industries. Applications that consistently used Alloy 347 include: High temperature chemical processes |